mig wire
Forum rules
By using this site, you agree to our rules. Please see: Terms of Use
By using this site, you agree to our rules. Please see: Terms of Use
-
- Minor Legend
- Posts: 1182
- Joined: Wed Aug 12, 2009 7:38 pm
- MMOC Member: Yes
mig wire
what thickness mig wore should i use for:
-chassis
-body panels
-chassis
-body panels
Using 0.6mm made me think that my Sip welder was as bad as a lot of people claim (mainly making frequent 'birds nests') - changing to 0.8 removed that problem altogether and I haven't used the thin stuff for years now. Wire feed mechanism in my new Sealey welder might handle it better, but I don't think I'll bother to find out!

I've never investigated what the proper distance from tip to the end of the outer shroud is recommended as, but on my, gulp, SIP, the two were nearly level, and the wire was always sticking. I made a distance piece to bring the outer shroud forward by about 3mm, and cured that one! (Still plenty more problems with that particular make, though!)Mick_Anik wrote:I've struggled with 0.6 - the wire kept sticking in the pistol tip. I tried all manner of different settings, with no improvement. So I use 0.8 all the time now, and it hardly ever sticks in the tip.
Funny business, welding!
-
- Minor Legend
- Posts: 1453
- Joined: Tue Jan 30, 2007 10:09 pm
- Location: Essex
- MMOC Member: No
I have only ever used .6 wire and never had a birds nest in the welder, I am however an expert on welding the wire to the tip!
I have virtually cured this by increasing the distance to the work not allowing the wire to burn back to the tip.
I have the wire drive set so that if I did get a tip weld the drive would slip without a problem.
I have virtually cured this by increasing the distance to the work not allowing the wire to burn back to the tip.
I have the wire drive set so that if I did get a tip weld the drive would slip without a problem.
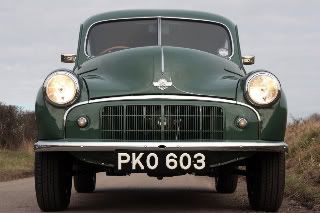