chassis leg
Forum rules
By using this site, you agree to our rules. Please see: Terms of Use
By using this site, you agree to our rules. Please see: Terms of Use
chassis leg
Hi. Can anyone help. how do i remove the old leg? i have a new one ready to install but unsure where to start.thanks
-
- Minor Legend
- Posts: 2180
- Joined: Fri May 30, 2008 9:41 pm
- Location: Sutton Coldfield
- MMOC Member: No
http://www.morrisminoroc.co.uk/index.ph ... c&start=60
Very photo heavy and eveline's friends took the engine out. Some may have tackled it with the engine in and supported. I'm unsure about this as I've never actually done the job.
Support the car on axle stands under the sills at the back of the front wheel arches, just where the front wing finishes underneath. Use some strong wood to spread the weight. This is because you won't be able to use the chassis legs. Chock the rear wheels front and back. Give car a good shake to convince yourself it's supported well.
Then you'll need to remove the eye bolts that bolt through the legs (possibly the torsion bars too, as they may get in the way). You will then take off the gearbox tunnel and remove the master cylinder and the pipework around it, then do something with the electrical cables that go to the rear. I think the clutch and brake pedal pivot will need to be removed. If just replacing the front section then this work can be reduced.
Then drill out the spot welds (from the top not underneath the car, you want to be above the car if it falls) and hope the leg drops away without too much force. Weld new one up using holes as the guide to positioning (the new one needs to be in the same place) use clamps and self tapers to help you pull the panels together. When welded up do the other side.
I'm sure if someones tackled it themselves, they'll give a few more details and issues they came across.
It's only attempting these kind of jobs that you learn.
Very photo heavy and eveline's friends took the engine out. Some may have tackled it with the engine in and supported. I'm unsure about this as I've never actually done the job.
Support the car on axle stands under the sills at the back of the front wheel arches, just where the front wing finishes underneath. Use some strong wood to spread the weight. This is because you won't be able to use the chassis legs. Chock the rear wheels front and back. Give car a good shake to convince yourself it's supported well.
Then you'll need to remove the eye bolts that bolt through the legs (possibly the torsion bars too, as they may get in the way). You will then take off the gearbox tunnel and remove the master cylinder and the pipework around it, then do something with the electrical cables that go to the rear. I think the clutch and brake pedal pivot will need to be removed. If just replacing the front section then this work can be reduced.
Then drill out the spot welds (from the top not underneath the car, you want to be above the car if it falls) and hope the leg drops away without too much force. Weld new one up using holes as the guide to positioning (the new one needs to be in the same place) use clamps and self tapers to help you pull the panels together. When welded up do the other side.
I'm sure if someones tackled it themselves, they'll give a few more details and issues they came across.
It's only attempting these kind of jobs that you learn.

My Minor:
A Clarendon Grey 1953 4 Door Series II.
MMOC - 66535
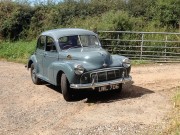
A Clarendon Grey 1953 4 Door Series II.
MMOC - 66535
-
- Minor Legend
- Posts: 2180
- Joined: Fri May 30, 2008 9:41 pm
- Location: Sutton Coldfield
- MMOC Member: No
My dad told me to do it this way when welding up the sills on mine. As long as one panel is a clearance hole and the other a pilot hole and deburred, you can close the panels right up tight. Reduces the opportunity for water ingress tooady4502 wrote:Great idea about the self tapers.

My Minor:
A Clarendon Grey 1953 4 Door Series II.
MMOC - 66535
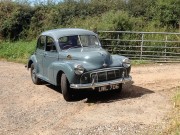
A Clarendon Grey 1953 4 Door Series II.
MMOC - 66535
-
- Moderator
- Posts: 7679
- Joined: Fri Nov 01, 2002 2:55 pm
- Location: LEAMINGTON SPA
- MMOC Member: No
If you're going to plug weld through holes, don't be tempted to drill them when both panels are together. Sometimes this will give a hevy drill burr that prevents the panels from closing right up.
Therefore it's better to have all holes drilled and burrs removed before you start welding.
Adding more when you've welded it on solid isn't usually a problem - mainly it's when you're at the part way stage when things can move.
Drilling out the old spotwelds is a good way to go as this should give enough holes for plug welding anyway. However, whenever i've tried this, there are always some extra spot welds out of sight / out of line that hold the darn thing together and make the job last twice as long.
Therefore it's better to have all holes drilled and burrs removed before you start welding.
Adding more when you've welded it on solid isn't usually a problem - mainly it's when you're at the part way stage when things can move.
Drilling out the old spotwelds is a good way to go as this should give enough holes for plug welding anyway. However, whenever i've tried this, there are always some extra spot welds out of sight / out of line that hold the darn thing together and make the job last twice as long.
Ray. MMOC#47368. Forum moderator.
Jan 06: The Minor SII Africa adventure: http://www.minor-detour.com
Oct 06: back from Dresden with my Trabant 601 Kombi
Jan 07: back from a month thru North Africa (via Timbuktu) in a S3 Landy
June 07 - back from Zwickau Trabi Treffen
Aug 07 & Aug 08 - back from the Lands End to Orkney in 71 pickup
Sept 2010 - finally gave up breaking down in a SII Landy...
where to break down next?
2013... managed to seize my 1275 just by driving it round the block
Jan 06: The Minor SII Africa adventure: http://www.minor-detour.com
Oct 06: back from Dresden with my Trabant 601 Kombi
Jan 07: back from a month thru North Africa (via Timbuktu) in a S3 Landy
June 07 - back from Zwickau Trabi Treffen
Aug 07 & Aug 08 - back from the Lands End to Orkney in 71 pickup
Sept 2010 - finally gave up breaking down in a SII Landy...
where to break down next?
2013... managed to seize my 1275 just by driving it round the block

so have i got this right? . i have a spot weld drill bit. i drill out the old spot welds, the leg should fall out then i line up my new leg and plug weld the old spot welds? everything on this car has taken twice a long anyway nothing new there. it has been sat in a shed for 28 years so you can guess what it is like.
-
- Minor Legend
- Posts: 2180
- Joined: Fri May 30, 2008 9:41 pm
- Location: Sutton Coldfield
- MMOC Member: No
Basically yes, you may need a cold chisel to help the old panel come away. Also you may need to jack up the new chassis leg or clamp it somehow to position it. Then using the big drilled holes as a guide to mark where you have to drill through the new chassis leg with a pilot drill for the self tappers. Take the chassis leg off and pilot drill where marked and deburr. Deburr under the floor and engine bay where the leg is to be attached. Then self tapper the leg up, you may need to use a washer on the self taper or a large headed screw. When up and happy with positioning, take out a self taper and plug weld through the large hole, filling the little one up too. Remember to make sure all metal is shiney where it is to be welded. Do one hole at a time, put self tapper back into box for use another day. 

My Minor:
A Clarendon Grey 1953 4 Door Series II.
MMOC - 66535
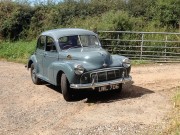
A Clarendon Grey 1953 4 Door Series II.
MMOC - 66535
Here's a tip on welding........
It's a battle - always! There comes a moment, after lots of hard slog and discomfort, when there is finally no doubt at all in your mind that all is ready for welding. A moment when all the little niggling doubts disappear. A moment when you know you have everything lined up, and that there's nothing more you can do to make anything better.
Weld away!
If you are still thinking: "What if I try............", then you are not ready to weld it up. Jiggle on, and wait for that moment.
Simple really, but Clapton would say that about playing live at the Albert Hall :D !
It's a battle - always! There comes a moment, after lots of hard slog and discomfort, when there is finally no doubt at all in your mind that all is ready for welding. A moment when all the little niggling doubts disappear. A moment when you know you have everything lined up, and that there's nothing more you can do to make anything better.
Weld away!
If you are still thinking: "What if I try............", then you are not ready to weld it up. Jiggle on, and wait for that moment.
Simple really, but Clapton would say that about playing live at the Albert Hall :D !