"*!!?***!#....C pillar repair section
Forum rules
By using this site, you agree to our rules. Please see: Terms of Use
By using this site, you agree to our rules. Please see: Terms of Use
-
- Minor Addict
- Posts: 859
- Joined: Sat Aug 19, 2006 9:30 pm
- Location: North Devon
- MMOC Member: No
I suggest we do what is done by the Jowett Javelin Owners club, most parts are hard to track down as it is. So members with original parts kindly take dimensions etc, and a profile is built up of the required part......mock ups produced etc. Then an order is taken for a certain number (and deposits taken), then the part is produced by a willing engineering company, trimmer, etc etc. The result is a properly fitting part made, to the original specs. It costs a bit more but by 'eck does it save some work!
Recently the JOC had some C pillar sections made, and 10 new Aluminium crankcases.
comments?
YG
Recently the JOC had some C pillar sections made, and 10 new Aluminium crankcases.
comments?
YG
Ultimate rust cure for your moggy....paint it brown, at least that way you dont notice the rust as much!!
-
- Minor Addict
- Posts: 859
- Joined: Sat Aug 19, 2006 9:30 pm
- Location: North Devon
- MMOC Member: No
Well, it seems to me that we might have an idea going. Next thing to do is make a list of the most commonly used parts that dont fit. Original part numbers would be handy too if we need to hunt down dimensional drawings etc.
YG
YG
Ultimate rust cure for your moggy....paint it brown, at least that way you dont notice the rust as much!!
The problem as I experience it is that Companies like Heritage and LMC are fully aware of the technical specification of panels, but lack the will to both renew old worn tooling or spend a bit of time in making sure that they are jigged properly.
If you present working drawings or even a sample to a manufacturer where is the money going to come from to produce the tooling, remember we were quoted a conservative £30,000 to tool up for a boot lid.
I think maybe on small items or engineered parts this approach is fine but the big manufacturers would be a totally different proposition.
We had new tooling made to re produce the external sunvisor clips to original spec, this alone cost over £600, we will not really recover the cost of this as the brackets themselves are sold at a token profit. If doing this in a proper business environment we would need to double the retail cost, which would in effect put customers off buying the product.
I agree totally with the idea of being able to say this what shape ,size, radius etc a part should be, but as the manufacturers already know this what prospect do we realistically have in persuading them to actually make the component correctly ,when they fail so spectaculary already.
I'm not sure that 'new' companies can be found in the UK who could fulfill the exacting standards that we require. A major company that we use has recently closed and this is echoed throughout the UK on a huge scale.
One option might be to go to eastern Europe, as did Frontline Costello for their MG panels. They are excellent quality but who would pay for the tooling and give them a promise of a substancial order to make it worth their while.
Sorry if this seems to be a pessimistic reply, but its based on years of experience of existing companies and personal experience of just how high the investment costs need to be.
If you present working drawings or even a sample to a manufacturer where is the money going to come from to produce the tooling, remember we were quoted a conservative £30,000 to tool up for a boot lid.
I think maybe on small items or engineered parts this approach is fine but the big manufacturers would be a totally different proposition.
We had new tooling made to re produce the external sunvisor clips to original spec, this alone cost over £600, we will not really recover the cost of this as the brackets themselves are sold at a token profit. If doing this in a proper business environment we would need to double the retail cost, which would in effect put customers off buying the product.
I agree totally with the idea of being able to say this what shape ,size, radius etc a part should be, but as the manufacturers already know this what prospect do we realistically have in persuading them to actually make the component correctly ,when they fail so spectaculary already.
I'm not sure that 'new' companies can be found in the UK who could fulfill the exacting standards that we require. A major company that we use has recently closed and this is echoed throughout the UK on a huge scale.
One option might be to go to eastern Europe, as did Frontline Costello for their MG panels. They are excellent quality but who would pay for the tooling and give them a promise of a substancial order to make it worth their while.
Sorry if this seems to be a pessimistic reply, but its based on years of experience of existing companies and personal experience of just how high the investment costs need to be.
-
- Minor Legend
- Posts: 1466
- Joined: Sat Aug 11, 2007 12:06 pm
- Location: Livingston Scotland
- MMOC Member: No
So we are basicaly stuffed when it comes to quality of body panels. Obviously certain people/companies have complained about the fit of the panels, and obviously the companies that make them aren't doing anything to improve the quality. Seems very much a catch 22 situation.
I guess those with the metal skills will repair panels rather than replace them. The big question has to be, if the manufacturers of these parts suffer reduced sales due to quality issues, will they invest in tooling to improve the panels, or go bust.
The only parts I have had problems with so far, are a grill surround trim, the chrome fell off after 6 months, and brake light switches.
I guess those with the metal skills will repair panels rather than replace them. The big question has to be, if the manufacturers of these parts suffer reduced sales due to quality issues, will they invest in tooling to improve the panels, or go bust.
The only parts I have had problems with so far, are a grill surround trim, the chrome fell off after 6 months, and brake light switches.
[img]http://i49.photobucket.com/albums/f264/Ghostrider117/sig.jpg[/img]
http://www.freewebs.com/moggytech
http://www.freewebs.com/moggytech
The big question has to be, if the manufacturers of these parts suffer reduced sales due to quality issues, will they invest in tooling to improve the panels, or go bust.
Afraid not, the companies involved in manufacturing the panels probably view the classic market as a 'charity' case as they make most profit from more modern models, so if the demand lessens they will simply stop production.
I am by no means damning the manufacturers, but from our stance we do seem to be a 'second best'
I believe that if we can set up a proper survey of opinions and experiences of problem parts then we can offer this to the relevant manufacturer along with a plea for better quality at an affordable price. If we do not then we might well loose the mass ability to re manufacture our chosen classic.
Frank, approaching an E European manufacturer is fine but where is the invesment going to come from. They would probably want a run of 100 pairs of a given panel before tooling, plus the cost of tooling, the money simply is not there from within the trade, so I feel that our only hope is careful informed discussion with the existing manufacturers in the UK.
I'll see if a questionaire can be inserted into Minor Matters, to gain a more representative and 'greater' response.
Afraid not, the companies involved in manufacturing the panels probably view the classic market as a 'charity' case as they make most profit from more modern models, so if the demand lessens they will simply stop production.
I am by no means damning the manufacturers, but from our stance we do seem to be a 'second best'
I believe that if we can set up a proper survey of opinions and experiences of problem parts then we can offer this to the relevant manufacturer along with a plea for better quality at an affordable price. If we do not then we might well loose the mass ability to re manufacture our chosen classic.
Frank, approaching an E European manufacturer is fine but where is the invesment going to come from. They would probably want a run of 100 pairs of a given panel before tooling, plus the cost of tooling, the money simply is not there from within the trade, so I feel that our only hope is careful informed discussion with the existing manufacturers in the UK.
I'll see if a questionaire can be inserted into Minor Matters, to gain a more representative and 'greater' response.
-
- Minor Legend
- Posts: 3798
- Joined: Tue Jul 25, 2006 9:46 am
- Location: Burnley
- MMOC Member: No
I would have thought there is a lot bigger market for Minor panels than for Jowett Javelin panels.
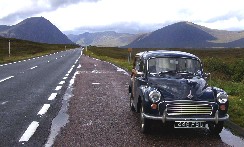
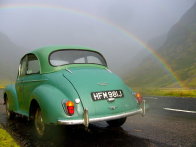
Alex Holden - http://www.alexholden.net/
If it doesn't work, you're not hitting it with a big enough hammer.
I'm doing my N/S sills, box section etc, A post bottom and C post bottom.
I agree with the C post repair section issue. There's going to have to be a lot of fettling to get that to fit. It's not even the right shape.
I'm thinking about welding new metal into the old post to try to get a better fit.
Andrew
I agree with the C post repair section issue. There's going to have to be a lot of fettling to get that to fit. It's not even the right shape.
I'm thinking about welding new metal into the old post to try to get a better fit.
Andrew