thinking ahead....
Forum rules
By using this site, you agree to our rules. Please see: Terms of Use
By using this site, you agree to our rules. Please see: Terms of Use
-
- Minor Legend
- Posts: 1395
- Joined: Sat Jan 06, 2007 3:55 pm
- Location: Raunds, Northamptonshire
- MMOC Member: No
thinking ahead....
Hi there,
I've spent this afternoon sweeping out the garage and whilst I did and in between the cups of tea that I hoped would be brought but weren't, I thought of 4 bodywork questions that I need help with before long...
1. Is there any reason why I shouldn't seam weld my new front chassis legs completely rather than spot or stitch weld?
2. The RH chassis leg repair section 32" long stops just at the clutch shaft bush (do you know what I mean?) but has an extra metal sleeve there to fit into the original remaining section and this will presumably need to be trimmed to fit. The repair section doesn't come with the bush holes already drilled-although the LHchassis leg does but with holes on the wrong side!
3. A general question now; on repair panels should I remove the black transport paint or can it be safely sprayed over?
4. When repairing outer panels like the lower panels behind the doors (2 door saloon) is it better/ neater to weld from inside out?
Forgive all these questions but the sun has suddenly caused my brain to start working again after the winter and I know this forum will provide the answers!
Many thanks
Alastair
I've spent this afternoon sweeping out the garage and whilst I did and in between the cups of tea that I hoped would be brought but weren't, I thought of 4 bodywork questions that I need help with before long...
1. Is there any reason why I shouldn't seam weld my new front chassis legs completely rather than spot or stitch weld?
2. The RH chassis leg repair section 32" long stops just at the clutch shaft bush (do you know what I mean?) but has an extra metal sleeve there to fit into the original remaining section and this will presumably need to be trimmed to fit. The repair section doesn't come with the bush holes already drilled-although the LHchassis leg does but with holes on the wrong side!
3. A general question now; on repair panels should I remove the black transport paint or can it be safely sprayed over?
4. When repairing outer panels like the lower panels behind the doors (2 door saloon) is it better/ neater to weld from inside out?
Forgive all these questions but the sun has suddenly caused my brain to start working again after the winter and I know this forum will provide the answers!
Many thanks
Alastair
]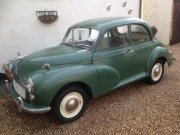
OK, here goes...
1 - seam welding will be fine from a strength point of view. As you say, not original but no problems with strength.
2 - Not sure what the question is...?
3 - Just rub it over with a scotch pad and prep in the usual way. Modern stuff is not as bad as it used to be which had to be all removed so unless they ae old repair panels then just prep as above....
4 - Whichever is easier to get to! Welds can always be dressed and filled to provide a neat finish....
1 - seam welding will be fine from a strength point of view. As you say, not original but no problems with strength.
2 - Not sure what the question is...?
3 - Just rub it over with a scotch pad and prep in the usual way. Modern stuff is not as bad as it used to be which had to be all removed so unless they ae old repair panels then just prep as above....
4 - Whichever is easier to get to! Welds can always be dressed and filled to provide a neat finish....
[sig]8426[/sig]
Compare the Minors - Simples !! http://mog.myfreeforum.org/index.php
Compare the Minors - Simples !! http://mog.myfreeforum.org/index.php
I'd add
1 - plug weld and seam weld, but not just seam. Seam welds are not that strong on their own but add strength to a plug or spot welded part.
3-we remove all black paint, mainly because we have to guarantee our work, and in the case of the C.Ware panels this is must, just to remove the surface rust.
1 - plug weld and seam weld, but not just seam. Seam welds are not that strong on their own but add strength to a plug or spot welded part.
3-we remove all black paint, mainly because we have to guarantee our work, and in the case of the C.Ware panels this is must, just to remove the surface rust.
-
- Moderator
- Posts: 7679
- Joined: Fri Nov 01, 2002 2:55 pm
- Location: LEAMINGTON SPA
- MMOC Member: No
Seam welding the edge of a lap joint means the 'box' of the box section is more floppy - you're unlikely to ever notice but from a strength point of view I'd add some plug welds or just plug weld it all.
I use an ø8mm drill bit - and buy in bulk. This way if you only use a sharp drill bit the preperation is done in minutes. These seem to MIG really well, as this gives enough space to make sure you are penetrating the other side before widening the weld pool to take in all the surrounding metal.
As for the missing fixings - are you sure you have the legs the right way round?? If so, then they are made wrong and you should chase the supplier for correct parts as (free) replacements.
Both legs had the clutch relay shaft mounting originally - replacement LH leg never seems to have these so it's rather unfair on people with LHD cars!
I use an ø8mm drill bit - and buy in bulk. This way if you only use a sharp drill bit the preperation is done in minutes. These seem to MIG really well, as this gives enough space to make sure you are penetrating the other side before widening the weld pool to take in all the surrounding metal.
As for the missing fixings - are you sure you have the legs the right way round?? If so, then they are made wrong and you should chase the supplier for correct parts as (free) replacements.
Both legs had the clutch relay shaft mounting originally - replacement LH leg never seems to have these so it's rather unfair on people with LHD cars!
Ray. MMOC#47368. Forum moderator.
Jan 06: The Minor SII Africa adventure: http://www.minor-detour.com
Oct 06: back from Dresden with my Trabant 601 Kombi
Jan 07: back from a month thru North Africa (via Timbuktu) in a S3 Landy
June 07 - back from Zwickau Trabi Treffen
Aug 07 & Aug 08 - back from the Lands End to Orkney in 71 pickup
Sept 2010 - finally gave up breaking down in a SII Landy...
where to break down next?
2013... managed to seize my 1275 just by driving it round the block
Jan 06: The Minor SII Africa adventure: http://www.minor-detour.com
Oct 06: back from Dresden with my Trabant 601 Kombi
Jan 07: back from a month thru North Africa (via Timbuktu) in a S3 Landy
June 07 - back from Zwickau Trabi Treffen
Aug 07 & Aug 08 - back from the Lands End to Orkney in 71 pickup
Sept 2010 - finally gave up breaking down in a SII Landy...
where to break down next?
2013... managed to seize my 1275 just by driving it round the block

-
- Moderator
- Posts: 7679
- Joined: Fri Nov 01, 2002 2:55 pm
- Location: LEAMINGTON SPA
- MMOC Member: No
based on mechanical engineering principles - where you make the join has an impact on the strength.Well you really got me now - I heard some tosh but if you seem weld both sides of the leg to the floor then no amount of additional strength will be effected by plug welding also.... !!!!!
A 4 sided box is stronger than a 6 sided one.
Plug welding takes the join to the inner edge of the lip - seam welding is only at the outer edge.
Last edited by rayofleamington on Sun Mar 29, 2009 8:16 pm, edited 1 time in total.
Ray. MMOC#47368. Forum moderator.
Jan 06: The Minor SII Africa adventure: http://www.minor-detour.com
Oct 06: back from Dresden with my Trabant 601 Kombi
Jan 07: back from a month thru North Africa (via Timbuktu) in a S3 Landy
June 07 - back from Zwickau Trabi Treffen
Aug 07 & Aug 08 - back from the Lands End to Orkney in 71 pickup
Sept 2010 - finally gave up breaking down in a SII Landy...
where to break down next?
2013... managed to seize my 1275 just by driving it round the block
Jan 06: The Minor SII Africa adventure: http://www.minor-detour.com
Oct 06: back from Dresden with my Trabant 601 Kombi
Jan 07: back from a month thru North Africa (via Timbuktu) in a S3 Landy
June 07 - back from Zwickau Trabi Treffen
Aug 07 & Aug 08 - back from the Lands End to Orkney in 71 pickup
Sept 2010 - finally gave up breaking down in a SII Landy...
where to break down next?
2013... managed to seize my 1275 just by driving it round the block

'Tosh !', sorry just basic bodyshop rules. Manufactures spend many hours deciding on how best to join materials and with chassis the importance is strength of joint, hence spot welds as they cover a wide surface area when correctly spaced.
My suggestion of seaming the edges as well will add some additional strength to the existing join. but on its own it does not provide a suitable ,strong joint .
You will find that in many bodyshops dealing with modern cars that only spot welds are allowed, infact the welders now simply pickup the spot welder , type in the make and model of the car and the area being repaired and the spot welder will instruct you where to weld. Porsche have always been very insistant on welding practice and always inspected the work ,any additional welding was rejected and the piece was re done.
My suggestion of seaming the edges as well will add some additional strength to the existing join. but on its own it does not provide a suitable ,strong joint .
You will find that in many bodyshops dealing with modern cars that only spot welds are allowed, infact the welders now simply pickup the spot welder , type in the make and model of the car and the area being repaired and the spot welder will instruct you where to weld. Porsche have always been very insistant on welding practice and always inspected the work ,any additional welding was rejected and the piece was re done.
Right then boys, lets not get into body torsional stiffness as this is an area that I know quite a bit about. Indeed, if you spot welded one area as opposed to seem welding then the torsional stiffness would be decreased in the area of welding but may well be increased in other areas. When the Minor was built it wasn't a science - just a practicality and indeed in many cases today it is a trade off between ease (and costs) of manuafacturing against ultimate (desired) stiffness. Half a dozen spot welds along the length of the chassis leg will never be as strong as both edges seem welded, period... However, as has been said before this is my opinion (based on 25 yers of motor manufacture) and is to be taken as desired by anyone reading this.
[sig]8426[/sig]
Compare the Minors - Simples !! http://mog.myfreeforum.org/index.php
Compare the Minors - Simples !! http://mog.myfreeforum.org/index.php
But we are not talking about 'half a dozen spot welds' - there should be many many spot welds! Every inch I would say. Seam welding the edges gives no real strength - and certainly v little torsional stiffness. The spot welds clamp the flat srfaces of the cahssis leg up against the floor - completing the box - and if done properly will give excellent torsional stiffness !



The reason for seaming the edge as well as having the original spot welds is to assist the strength of the leg and reduce the tendancy for the chassis legs (in particular) to pop the spot welds when large capacity high torque engines are fitted. This practice 'does 'work very well in achieving this and I agree that the seam weld offers little in the way of torsional stiffness.
The trouble with just seam welding is that you only weld a small proportion of the flange/floor, where with spot welds/plug welds these offer a much greater anchorage over a large proportion of the mating surfaces.
The trouble with just seam welding is that you only weld a small proportion of the flange/floor, where with spot welds/plug welds these offer a much greater anchorage over a large proportion of the mating surfaces.
-
- Moderator
- Posts: 7679
- Joined: Fri Nov 01, 2002 2:55 pm
- Location: LEAMINGTON SPA
- MMOC Member: No
Anyone who fitted a chassis leg with half a dozen spot welds deserves very severe treatment! I go for about every 1.5" or every 3" if it's seam welded.However in areas where you can seam weld the inner edge of a lip - that will be good. The issue comes on a box section with a lap joint where the inner edge is not accessible.Half a dozen spot welds along the length of the chassis leg will never be as strong as both edges seem welded, period...
Like I said, the difference is not massive - but there is a difference.you're unlikely to ever notice
Chassis stiffness was not a 'science' in the 40's but was already being developed into one. The team who produced the Minor design included engineers who had spent many years investigating 'frame stiffness' (shell stiffness in more modern terms). For the UK they were pioneers (and did a fantastic job too!) although the French were already ahead of them in monocoque design (I think the term 'monocoque' was originaly French but i'm only guessing that)
For the Minor, Spot welding wasn't the only method available - some areas of the Minor are seam welded.
Seam welding 'both edges'? I'm lost on this discussion - the chassis leg has 2 edges. You can't accesss the inside of the leg so i can't see you meant to seam weld both edges of both lips.
Ray. MMOC#47368. Forum moderator.
Jan 06: The Minor SII Africa adventure: http://www.minor-detour.com
Oct 06: back from Dresden with my Trabant 601 Kombi
Jan 07: back from a month thru North Africa (via Timbuktu) in a S3 Landy
June 07 - back from Zwickau Trabi Treffen
Aug 07 & Aug 08 - back from the Lands End to Orkney in 71 pickup
Sept 2010 - finally gave up breaking down in a SII Landy...
where to break down next?
2013... managed to seize my 1275 just by driving it round the block
Jan 06: The Minor SII Africa adventure: http://www.minor-detour.com
Oct 06: back from Dresden with my Trabant 601 Kombi
Jan 07: back from a month thru North Africa (via Timbuktu) in a S3 Landy
June 07 - back from Zwickau Trabi Treffen
Aug 07 & Aug 08 - back from the Lands End to Orkney in 71 pickup
Sept 2010 - finally gave up breaking down in a SII Landy...
where to break down next?
2013... managed to seize my 1275 just by driving it round the block

-
- Minor Friendly
- Posts: 71
- Joined: Sun Mar 22, 2009 11:12 pm
- Location: Ringwood
- MMOC Member: No